Shaft Seal |
Description |
Advantages |
Disadvantages |
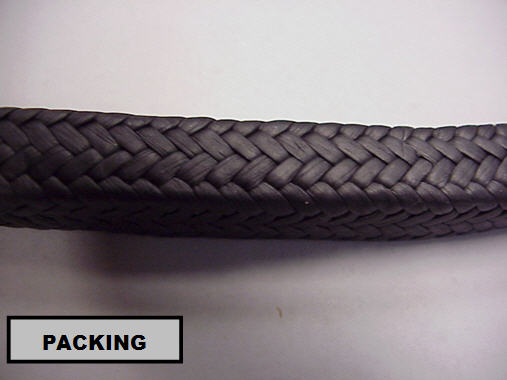 |
Braided
or formed rings that are compressed in the stuffing box of the pump.
As the packing is tightened, it compresses against the shaft and
stuffing box bore to create the seal. |
- Economical
- Excellent for sealing thick,
difficult to seal liquids such as chocolate, molasses, asphalt,
resins, tar, and some adhesives
- Seldom catastrophically fails
|
- Poor seal for thin liquids,
especially at higher pressures
- Requires lubrication either
externally or by the liquid being pumped; this means packing must be
allowed to leak slightly (weep)
- Can damage the pump shaft if
adjusted too tightly
|
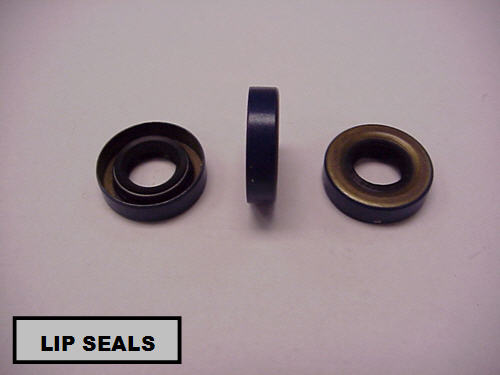 |
A
circular elastomeric seal element in a rigid outer housing |
- Economical
- Come in a wide variety
including cartridge triple lip seals for higher viscosity liquids
|
- Typically limited to lower
pressures
- Poor for thin, non-lubricating
liquids or for abrasives
- Can catastrophically fail
|
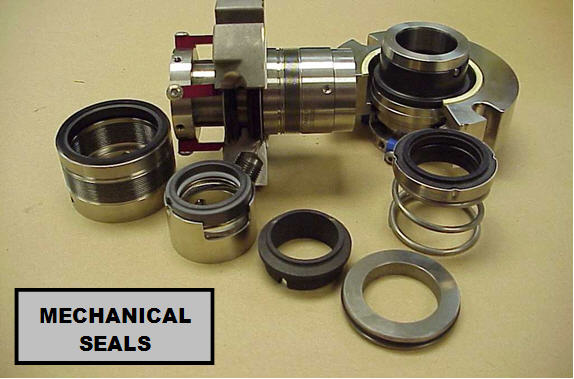 |
Simplified, mechanical seals use highly polished faces (one stationary
and one rotating) running against each other* to form a seal.
*actually, seal faces only
touch when at rest. While turning, they are separated by a thin
film of the liquid being pumped, barrier fluid, or gas |
- Mechanical seals come in a
wide variety of designs and materials for nearly every application.
- Offer designs which can be
easily replaced or repaired
|
- Like lip seals, can
catastrophically fail
- Higher end double cartridge
seals and gas barrier seals are quite expensive and require external
support equipment.
|
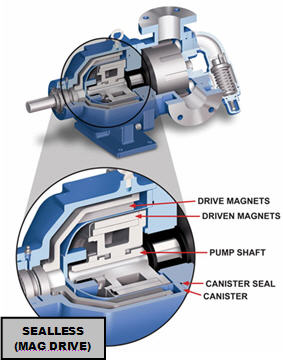 |
A Mag
Drive pump is a sealless pump that utilizes a magnetic coupling to
create a static shaft seal. Drive magnets (outer) align with
driven magnets (inner) and use magnetic force to turn the shaft through
a static containment shell (canister). |
- Mag Drive pumps are a truly
sealless design which ensures zero leakage of liquid or emissions,
making them ideal for hazardous, toxic, corrosive, flammable, or
expensive liquids.
- Extremely reliable for maximum
insurance against seal leakage and maximum seal life
|
- More expensive than most shaft
seal options, but this must also be weighed against the added costs
of seal replacement, including labor and cleanup.
- Typically limited to about
500°F / 260°C maximum (heat can permanently damage the magnets)
- Based on the cost and risk of
damage due to heat, monitoring devices are typically recommended to
protect these pumps from damage.
|